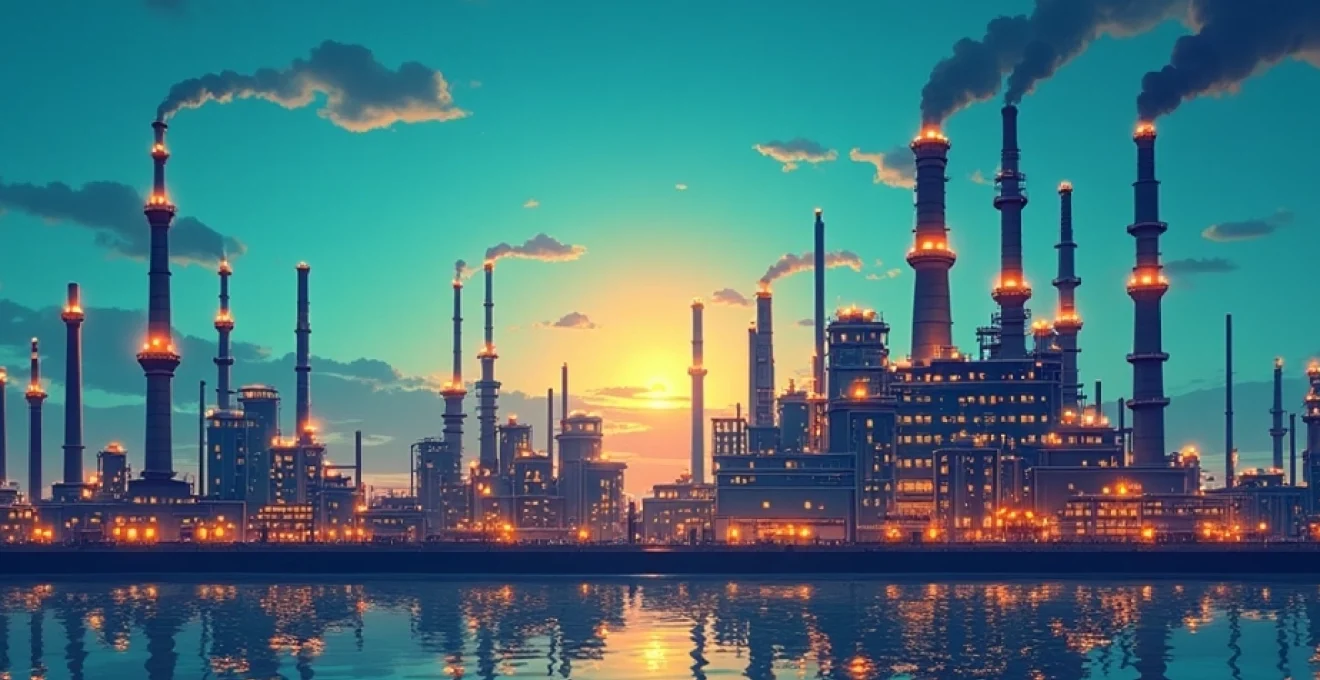
In today's competitive industrial landscape, energy efficiency has become a critical factor in determining the success and sustainability of manufacturing operations. As energy costs continue to rise and environmental regulations become more stringent, industries are increasingly focused on implementing strategies to optimize their energy consumption. This not only reduces operational expenses but also minimizes environmental impact, enhances productivity, and improves overall competitiveness.
Energy auditing and consumption analysis techniques
The foundation of any successful energy efficiency program lies in a comprehensive understanding of current energy consumption patterns. Energy auditing and consumption analysis techniques provide invaluable insights into where and how energy is being used within industrial facilities. These techniques involve a systematic examination of energy flows throughout the production process, identifying areas of waste and inefficiency.
One of the most effective tools in this regard is the energy balance sheet, which provides a detailed breakdown of energy inputs and outputs across different processes and equipment. This allows managers to pinpoint specific areas where energy is being lost or underutilized, enabling targeted interventions for maximum impact.
Another crucial technique is benchmarking, which involves comparing energy performance metrics against industry standards or best practices. This helps industries understand how their energy efficiency measures up to their peers and identifies opportunities for improvement. Advanced software tools can facilitate this process by automating data collection and analysis, providing real-time insights into energy consumption patterns.
Effective energy auditing is not a one-time event but an ongoing process of monitoring, analysis, and continuous improvement.
By implementing regular energy audits and leveraging sophisticated analysis techniques, industries can create a solid foundation for their energy efficiency initiatives, ensuring that resources are allocated to the areas with the greatest potential for improvement.
Advanced process optimization for industrial energy efficiency
Once energy consumption patterns have been thoroughly analyzed, the next step is to optimize industrial processes for maximum energy efficiency. This involves a range of advanced techniques and methodologies designed to streamline operations, reduce waste, and enhance overall energy performance.
Pinch analysis for heat integration in manufacturing
Pinch analysis is a powerful tool for optimizing heat exchange networks in industrial processes. This technique identifies opportunities to recover and reuse waste heat, significantly reducing the overall energy requirements of a manufacturing system. By analyzing the temperature profiles of hot and cold streams within a process, engineers can design heat exchanger networks that maximize energy recovery and minimize utility consumption.
The implementation of pinch analysis can lead to substantial energy savings, particularly in industries with high thermal energy demands such as chemical processing, oil refining, and food production. In some cases, energy reductions of up to 30% have been achieved through the strategic application of this technique.
Six sigma methodology for energy waste reduction
The Six Sigma methodology, originally developed for quality management, has proven to be an effective approach for reducing energy waste in industrial settings. By applying the DMAIC (Define, Measure, Analyze, Improve, Control) framework to energy efficiency initiatives, industries can systematically identify and eliminate sources of energy waste.
This data-driven approach involves setting clear energy performance targets, measuring current consumption levels, analyzing root causes of inefficiencies, implementing targeted improvements, and establishing control mechanisms to maintain gains over time. The rigorous statistical analysis inherent in Six Sigma helps ensure that energy efficiency efforts are focused on the most impactful areas, maximizing return on investment.
Real-time process control systems and machine learning algorithms
The advent of Industry 4.0 technologies has opened up new possibilities for real-time process control and optimization. Advanced sensors and IoT
devices can now collect vast amounts of data on energy consumption and process parameters, which can be analyzed using sophisticated machine learning algorithms to identify patterns and optimize operations in real-time.
These systems can automatically adjust process parameters to maintain optimal energy efficiency under varying conditions, responding to changes in production demands, ambient temperatures, or raw material characteristics. By leveraging the power of artificial intelligence, industries can achieve unprecedented levels of energy efficiency and process stability.
Exergy analysis for maximum thermodynamic efficiency
Exergy analysis takes energy efficiency considerations to a deeper level by examining not just the quantity of energy used, but also its quality or potential to do useful work. This approach recognizes that not all forms of energy are equally valuable from a thermodynamic perspective and seeks to optimize the use of high-quality energy sources.
By conducting exergy analyses of industrial processes, engineers can identify opportunities to match energy quality with process requirements more effectively. This might involve cascading energy use, where high-quality energy sources are used for high-temperature processes before being redirected to lower-temperature applications, maximizing overall thermodynamic efficiency.
Advanced process optimization techniques are not just about reducing energy consumption; they're about fundamentally rethinking how energy flows through industrial systems to maximize value and minimize waste.
High-efficiency equipment and technology implementation
While process optimization can yield significant energy savings, the implementation of high-efficiency equipment and technologies is often necessary to achieve truly transformative results. These advanced solutions can dramatically reduce energy consumption across a wide range of industrial applications.
Variable frequency drives (VFDs) in motor systems
Electric motors are ubiquitous in industrial settings, powering everything from pumps and fans to conveyor belts and compressors. Variable Frequency Drives (VFDs) offer a powerful solution for optimizing the energy efficiency of these motor systems. By allowing motors to operate at variable speeds based on actual load requirements, VFDs can significantly reduce energy consumption, particularly in applications with variable flow or pressure demands.
The energy savings potential of VFDs is substantial, with reductions of 30-50% being common in many applications. Beyond energy savings, VFDs also offer benefits such as improved process control, reduced mechanical stress on equipment, and lower maintenance costs.
Combined heat and power (CHP) systems for industrial applications
Combined Heat and Power (CHP) systems, also known as cogeneration, represent a highly efficient approach to energy production in industrial settings. These systems simultaneously generate electricity and useful thermal energy from a single fuel source, achieving overall efficiencies of up to 80% compared to around 50% for conventional separate heat and power systems.
CHP systems are particularly well-suited to industries with significant thermal energy requirements, such as food processing, chemicals, and pulp and paper. By producing both electricity and heat on-site, these systems can reduce reliance on grid electricity, lower energy costs, and improve energy security.
Advanced compressed air systems and leak detection technologies
Compressed air is often referred to as the "fourth utility" in industrial settings due to its widespread use. However, compressed air systems can be notoriously inefficient, with energy losses of up to 30% due to leaks alone being common. Advanced compressed air systems incorporate features such as variable speed compressors, sophisticated control systems, and heat recovery units to maximize efficiency.
Complementing these systems, cutting-edge leak detection technologies using ultrasonic sensors and artificial intelligence can identify and quantify air leaks with unprecedented accuracy. Some of these systems can even pinpoint leaks in real-time, allowing for immediate intervention and continuous optimization of compressed air networks.
Energy-efficient lighting solutions: LED and smart control systems
While lighting may not be the largest energy consumer in most industrial settings, it still represents a significant opportunity for efficiency improvements. LED lighting technology offers energy savings of up to 75% compared to traditional lighting systems, along with longer lifespans and improved light quality.
When combined with smart control systems that adjust lighting levels based on occupancy, daylight availability, and task requirements, the energy savings potential is even greater. These intelligent lighting systems not only reduce energy consumption but can also enhance worker productivity and safety by providing optimal lighting conditions at all times.
Waste heat recovery and utilization strategies
In many industrial processes, a significant portion of input energy is lost as waste heat. Implementing effective waste heat recovery and utilization strategies can dramatically improve overall energy efficiency by capturing this otherwise lost energy and putting it to productive use.
One of the most straightforward applications of waste heat recovery is preheating incoming materials or process fluids. For example, in a steel mill, exhaust gases from furnaces can be used to preheat scrap metal before it enters the melting process, reducing the energy required for melting. Similarly, in food processing plants, waste heat from refrigeration systems can be used to preheat water for cleaning operations.
More advanced waste heat recovery systems can convert low-grade thermal energy into electricity using technologies such as Organic Rankine Cycle (ORC) systems. These systems are particularly valuable in industries with large amounts of low-temperature waste heat, such as cement production or glass manufacturing.
Another innovative approach is the use of absorption chillers, which can convert waste heat into cooling energy. This technology is especially beneficial in industries that have simultaneous heating and cooling requirements, such as chemical processing or food and beverage production.
Waste heat recovery is not just about energy efficiency; it's about recognizing that every joule of energy has value and finding creative ways to harness that value throughout the industrial process.
Energy management systems (EMS) and ISO 50001 implementation
To truly embed energy efficiency into the DNA of industrial operations, a systematic approach to energy management is essential. Energy Management Systems (EMS) provide a structured framework for continuously improving energy performance, integrating energy considerations into all aspects of business operations.
SCADA systems for real-time energy monitoring
Supervisory Control and Data Acquisition (SCADA) systems form the backbone of modern industrial energy management. These systems collect and analyze real-time data from across the facility, providing operators and managers with a comprehensive view of energy consumption patterns. Advanced SCADA systems can integrate data from multiple sources, including production systems, utility meters, and environmental sensors, to provide a holistic picture of energy performance.
By leveraging machine learning
algorithms, SCADA systems can identify anomalies in energy consumption, predict future energy needs based on production schedules, and automatically optimize energy use across different processes. This real-time monitoring and control capability is crucial for maintaining peak energy efficiency in dynamic industrial environments.
Predictive maintenance algorithms for energy conservation
Predictive maintenance is a powerful tool for energy conservation in industrial settings. By using advanced analytics to predict when equipment is likely to fail or operate inefficiently, maintenance can be scheduled proactively, preventing energy waste due to poorly performing machinery.
These algorithms analyze data from sensors monitoring various parameters such as vibration, temperature, and power consumption to detect subtle changes that may indicate impending issues. By addressing these issues before they lead to significant energy waste or equipment failure, industries can maintain optimal energy efficiency while also reducing downtime and maintenance costs.
Employee engagement and training programs in energy management
While technology plays a crucial role in energy efficiency, the human factor cannot be overlooked. Effective energy management requires the active participation of employees at all levels of the organization. Comprehensive training programs can help employees understand the importance of energy efficiency, recognize opportunities for improvement in their daily work, and take ownership of energy-saving initiatives.
Some successful approaches include:
- Gamification of energy-saving efforts to encourage friendly competition between teams or departments
- Regular energy awareness campaigns highlighting the impact of individual actions on overall energy consumption
- Integration of energy efficiency metrics into performance evaluations and incentive structures
- Cross-functional energy teams to identify and implement energy-saving projects across different areas of the organization
By fostering a culture of energy awareness and continuous improvement, industries can tap into the collective creativity and problem-solving skills of their workforce to drive ongoing energy efficiency gains.
Renewable energy integration in industrial processes
As the cost of renewable energy technologies continues to decline, their integration into industrial processes is becoming an increasingly attractive option for enhancing energy efficiency and sustainability. While renewable energy may not directly improve the efficiency of industrial processes, it can significantly reduce overall energy costs and carbon footprint when implemented strategically.
Solar photovoltaic systems are particularly well-suited to many industrial applications, especially in regions with high solar irradiance. Large roof areas of factories and warehouses provide ideal locations for solar panel installations, which can generate a significant portion of a facility's electricity needs. In some cases, industrial sites with large land areas can even host utility-scale solar farms, potentially generating more electricity than they consume.
Wind energy is another viable option for industries located in areas with favorable wind resources. On-site wind turbines can provide a reliable source of renewable electricity, particularly when combined with energy storage systems to smooth out supply fluctuations.
For industries with high thermal energy requirements, solar thermal systems or biomass boilers can provide renewable heat for processes such as drying, sterilization, or space heating. These systems can be particularly effective when integrated with waste heat recovery systems to maximize overall energy efficiency.
The integration of renewable energy into industrial processes often requires careful planning and system design to ensure reliability and compatibility with existing operations. Advanced energy management systems that can balance multiple energy sources and optimize their use based on real-time conditions are crucial for maximizing the benefits of renewable energy integration.
As industries continue to push the boundaries of energy efficiency, the synergies between process optimization, high-efficiency technologies, waste heat recovery, systematic energy management, and renewable energy integration will become increasingly important. By adopting a holistic approach that leverages these diverse strategies, industries can achieve unprecedented levels of energy efficiency, reducing costs, enhancing competitiveness, and contributing to a more sustainable future.